Project MK7 GLI - Update 3 - FMIC And More
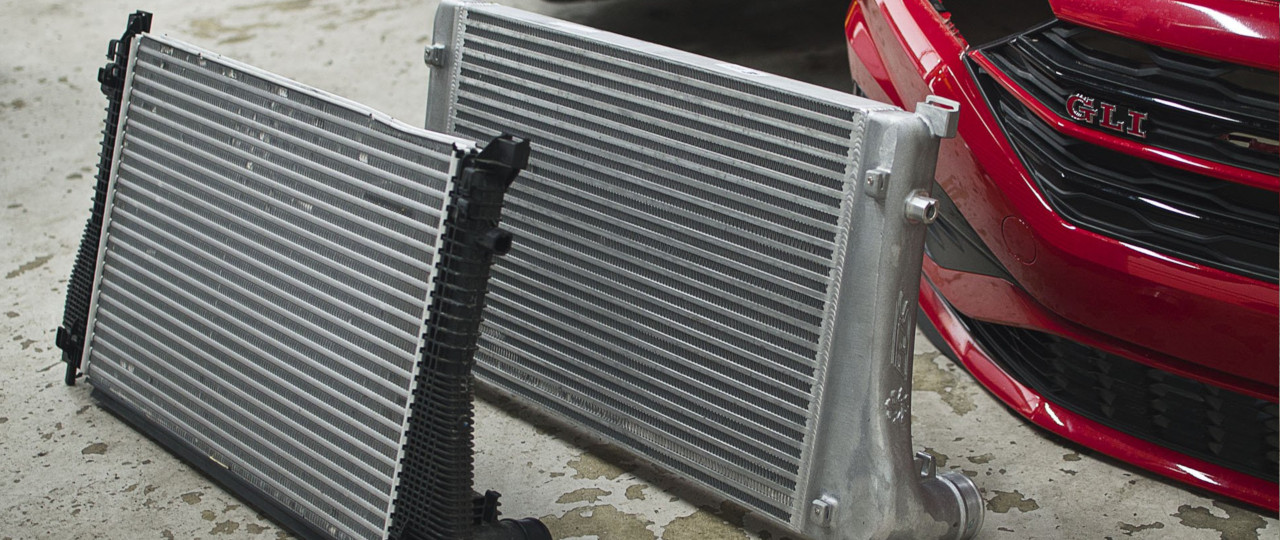
In preparation for our upcoming big turbo installation we knew that we had to have our bases covered. With any turbo upgrade, and even with the stock turbo, it's a great idea to upgrade your stock intercooler to one that is a bit more robust and up to the challenge of keeping those charge temperatures cooler. We chose the Integrated Engineering Intercooler for a variety of reasons, but not limited to its unique construction and fit and finish. It comes in at a very reasonable price point and includes everything necessary for installation while also being backed by proven results.
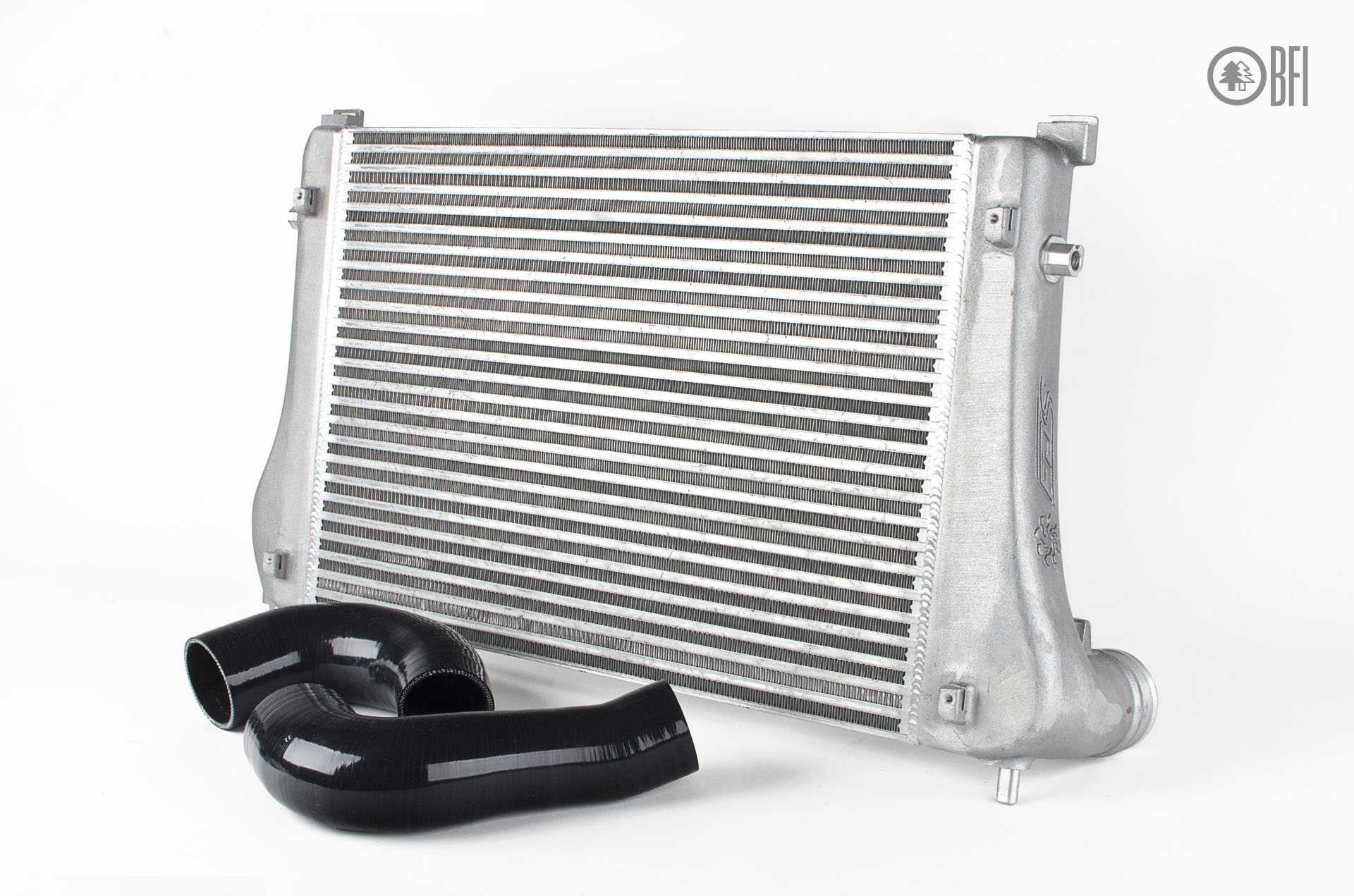
FDS (FLOW DISTRIBUTION SYSTEM)
The IE FDS (Flow Distribution System) has proven to distribute charge air uniformly across the inlet end of the core. In contrast to other intercoolers on the market which rely on natural airflow across the core, our FDS technology uses precisely shaped and placed fins cast into the intake plenum to fully take advantage of the large core volume effectively using the entire core. As a result, the IE FDS intercooler has been proven to reduce intake air temperatures more so than other units available, thus offering the largest power gains possible.
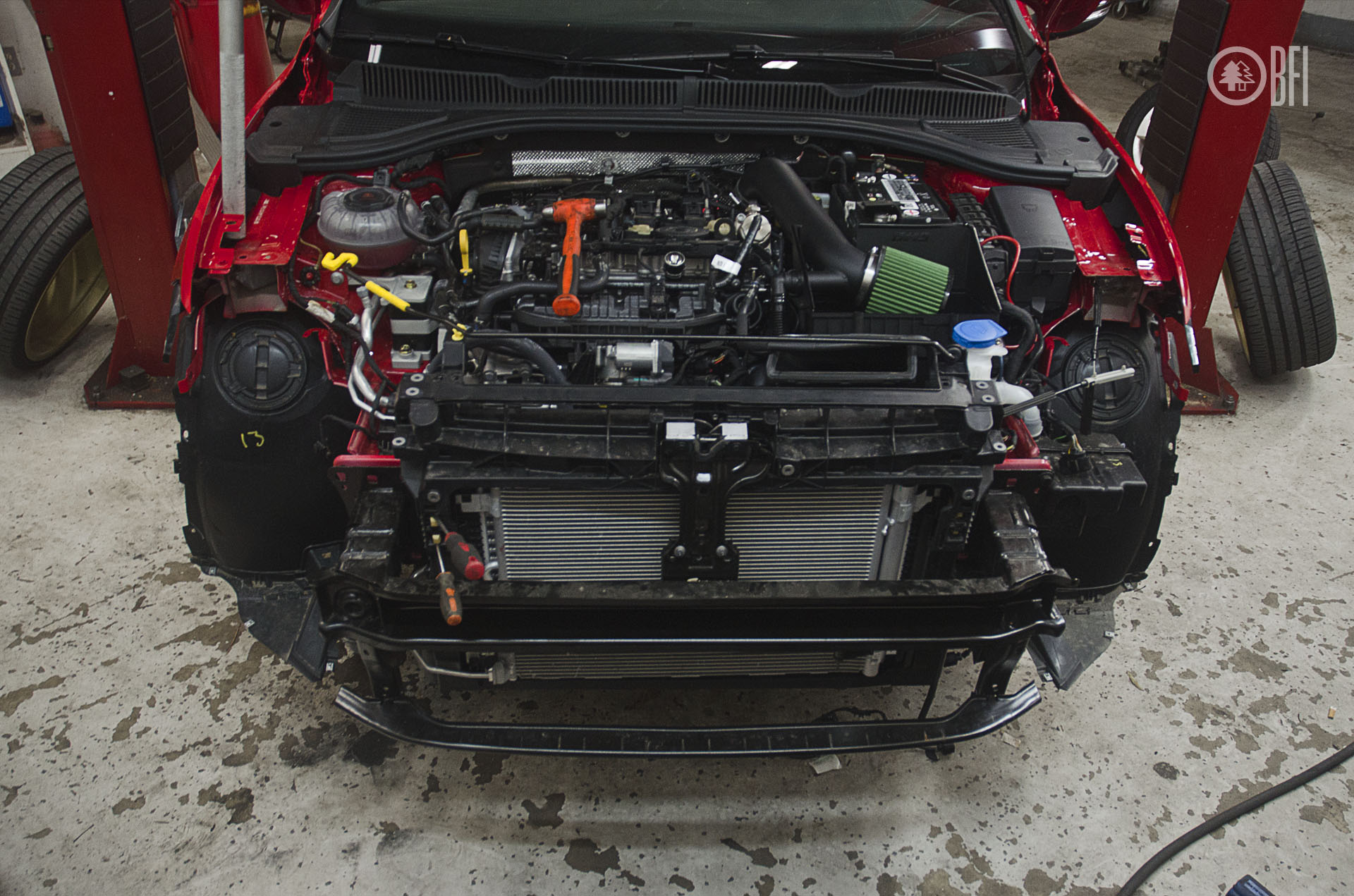
This intercooler is used in record-breaking cars! Increase horsepower and defeat heat soak with the IE front-mount Intercooler Kit for the MK7/MQB 2.0T EA888 Gen 3 engines.
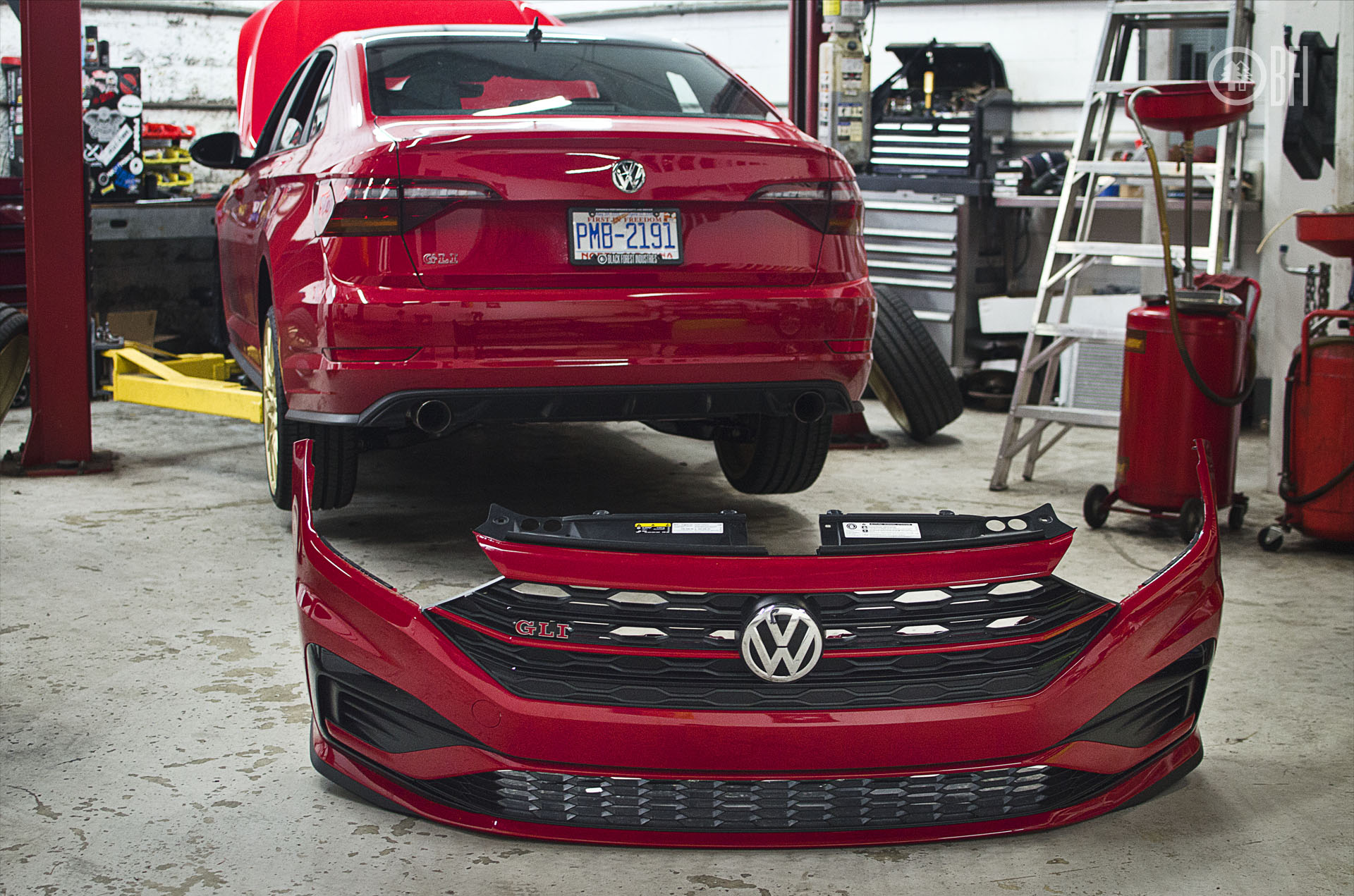
Unlike other intercoolers that are simply put together to fit on the car and offer a larger core, the IE FDS intercooler line receives special treatment from start to finish. The engineering department at IE used Computational Fluid Dynamics (CFD) software to optimize the end tanks and FDS system for minimum pressure drop and maximum flow. Once the end tanks had been designed and flow had been optimized, the 3D models headed over to their 3D printing studio to manufacture the initial prototype.
The 3D printed end tanks fastened onto a production core for testing. To validate the FDS technology, IE tested each model of intercooler in a controlled environment on their in-house engine dyno. A total of 16 temperature probes were placed on the core, with a column of 8 on either side. This allowed them to collect data at multiple points on the inlet side and outlet side of the intercooler to verify temperature distribution across the core. Once that data had been collected, it was analyzed and used to determine if changes in location or pitch of FDS channels were necessary before going to production.
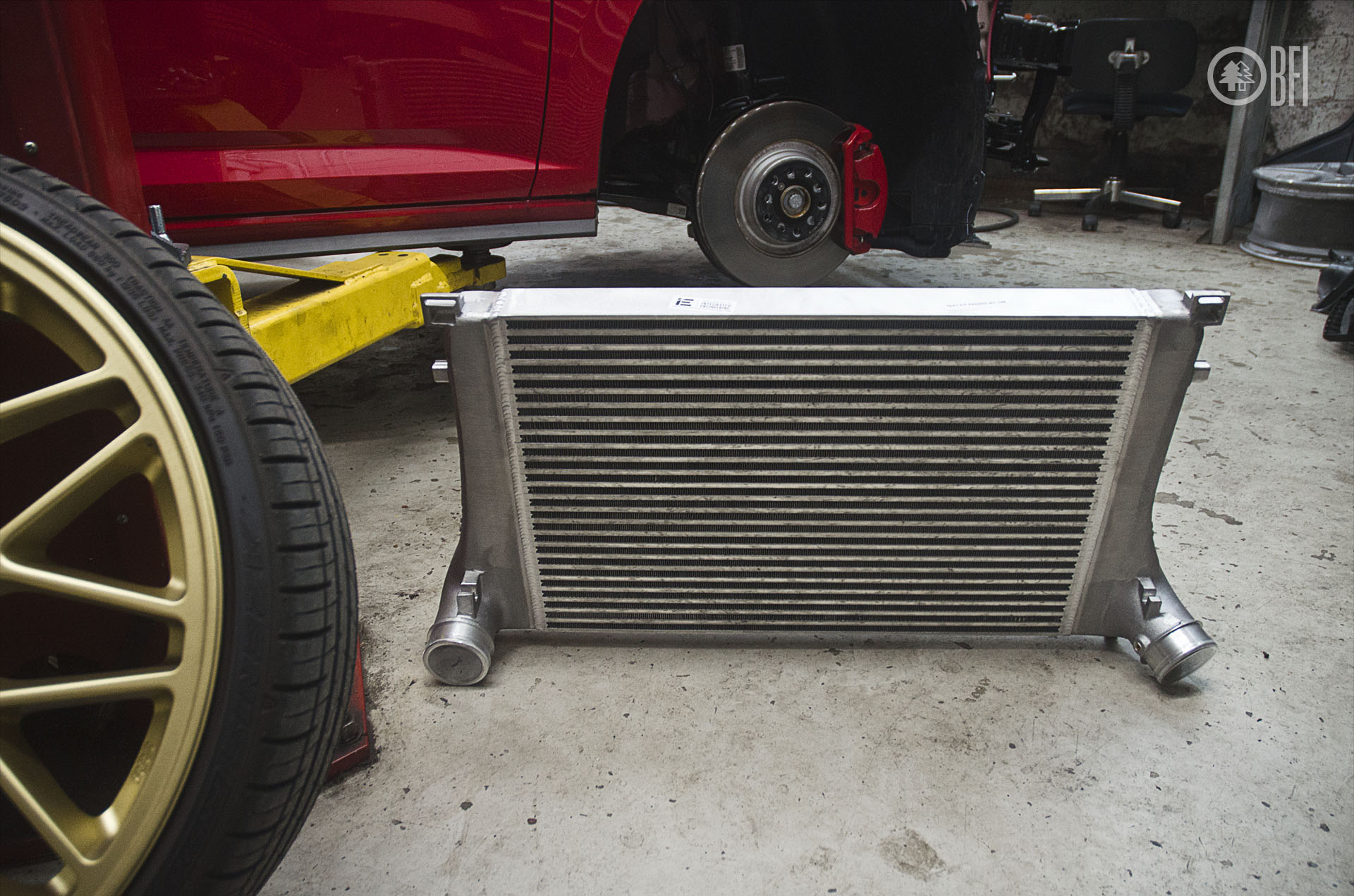
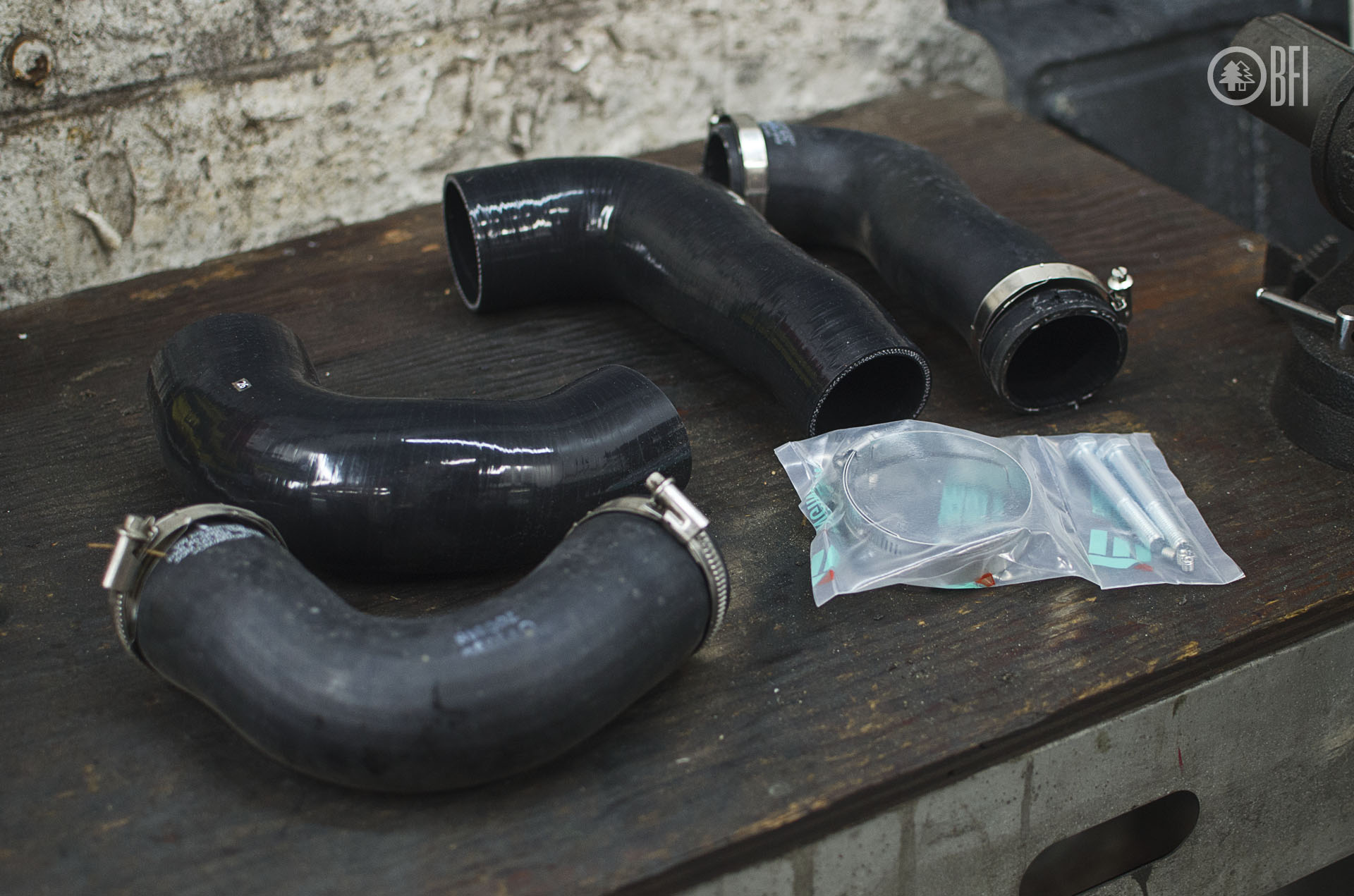
Included upgraded silicone hoses from Integrated replace the factory rubber hoses.
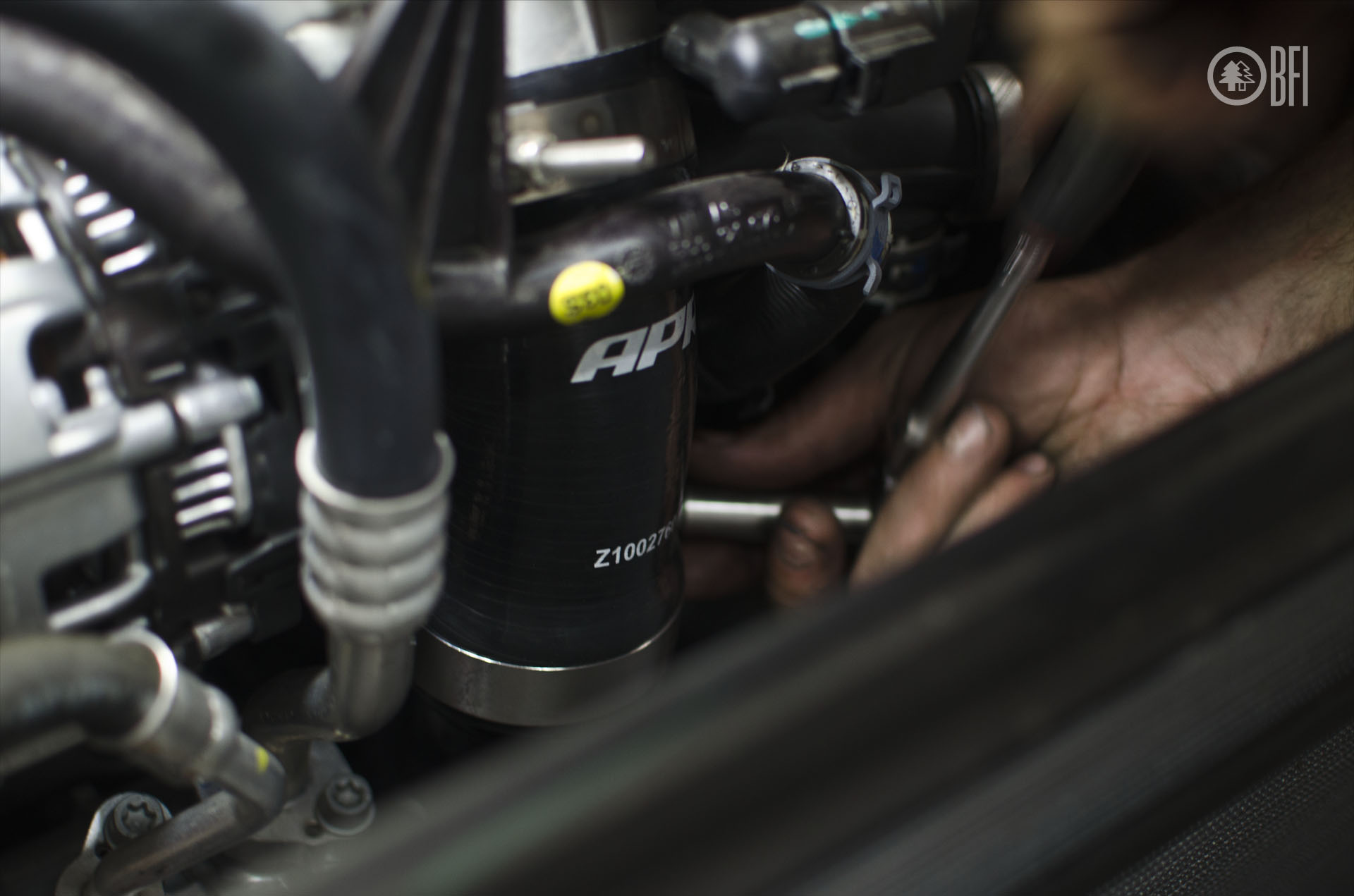
While we were at it, we also installed the silicone APR Throttle Body Hose to replace the factory rubber hose
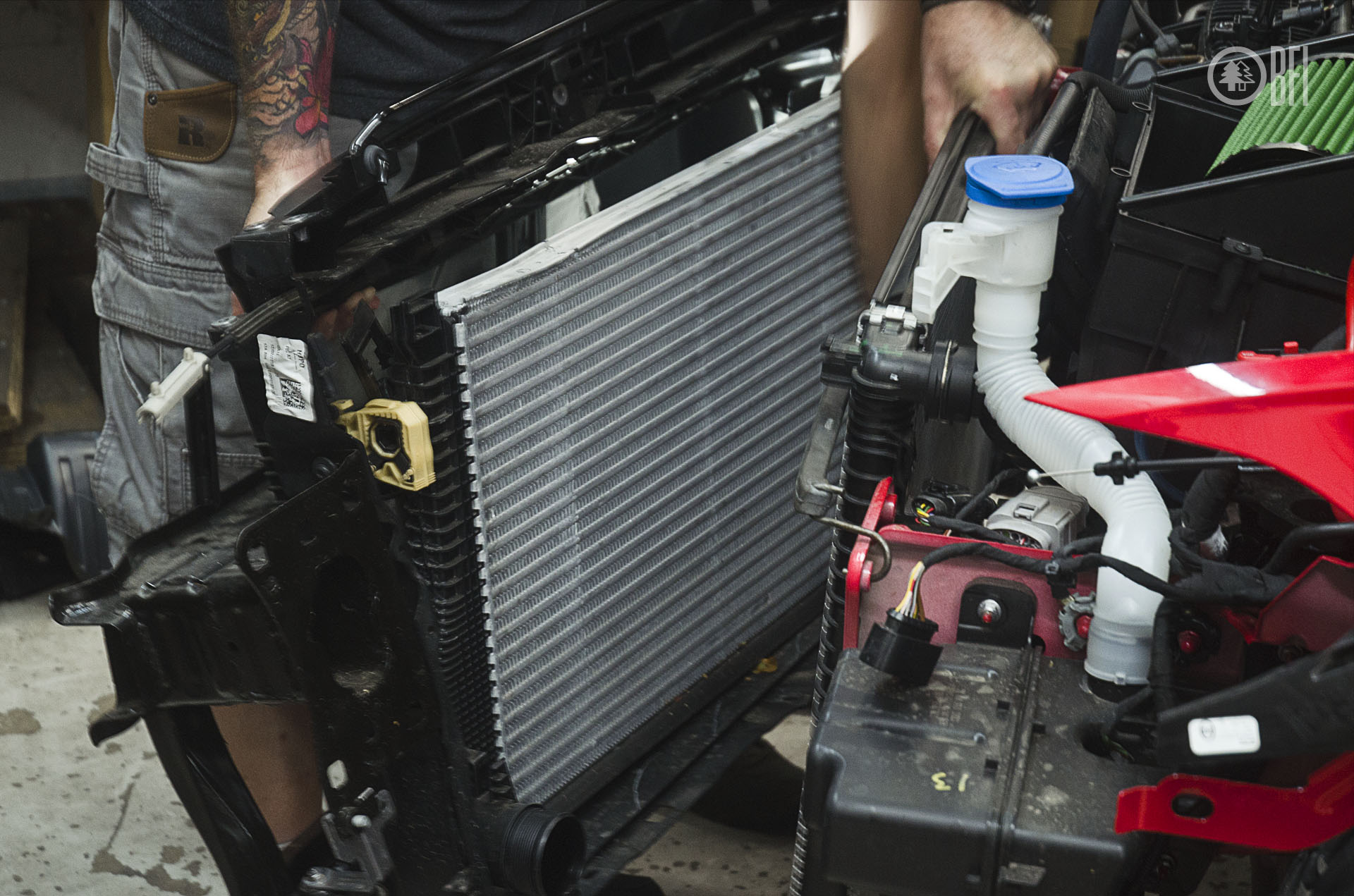
Exhaust
With few options available on the market and wanting specific requirements, we decided to take on the task of creating our own custom, one-off exhaust system. At the moment we do not have any immediate plans to product these for sale, but we will be extensively testing this design and set up to see if it is something that warrants further consideration. Choosing to utilize full stainless construction and multiple small resonators, we're aiming to increase flow without inducing unwanted drone or rasp.
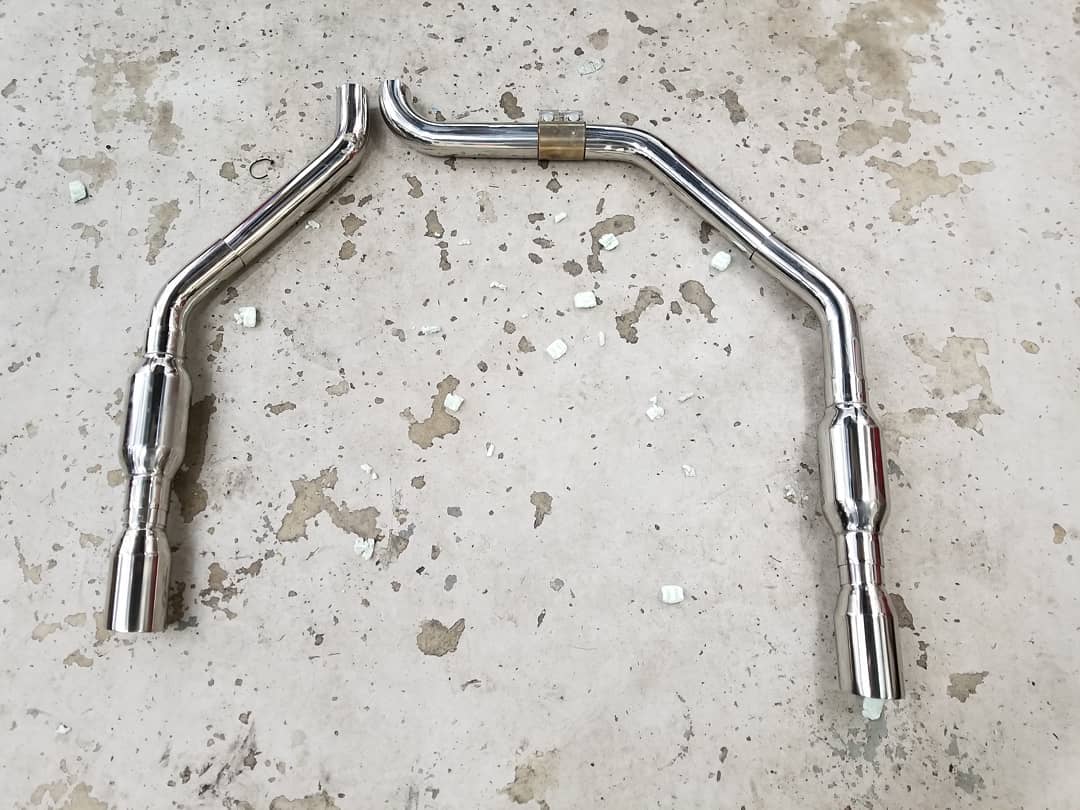
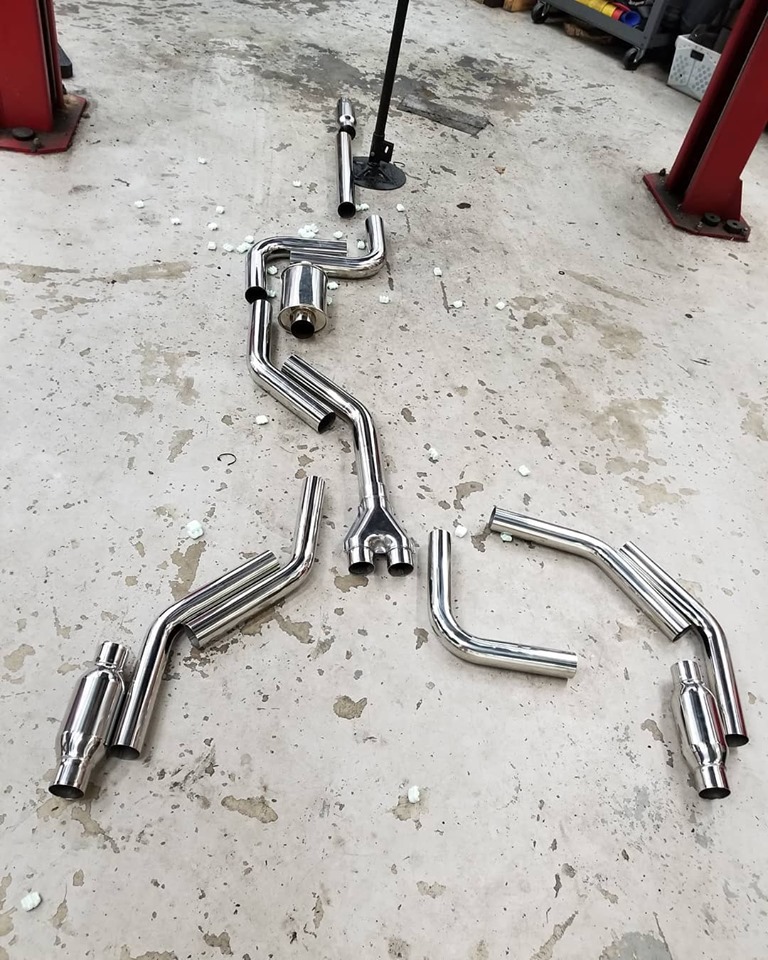
Laying out the overall path and design of the exhaust system. Our previously mapped out plan allows us to source off the shelf bends
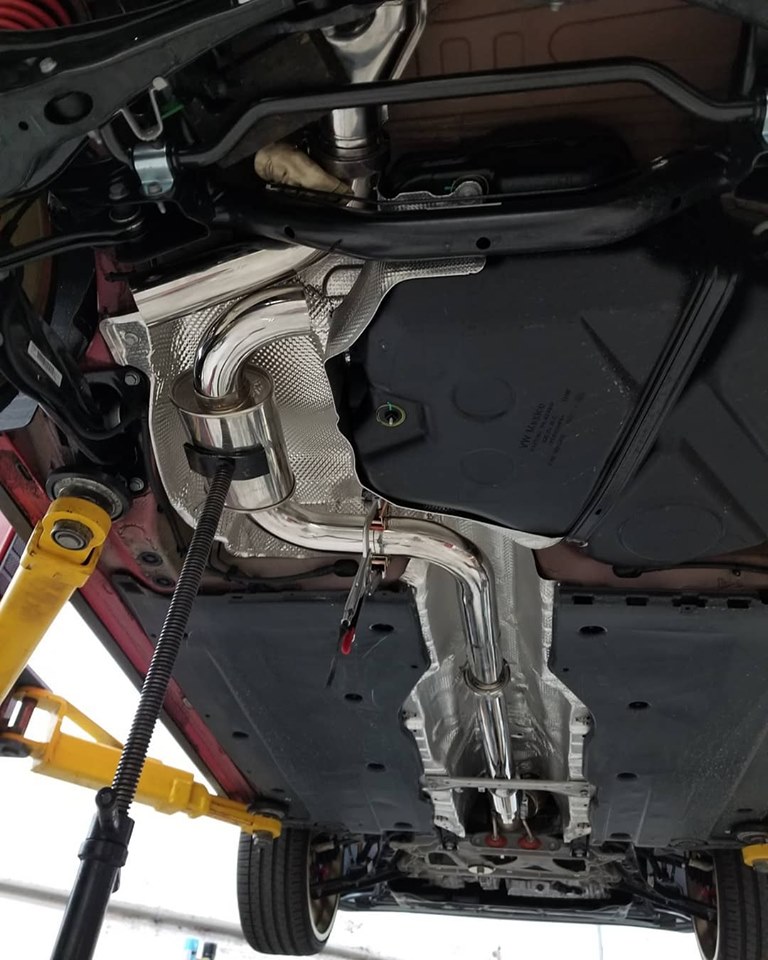
Careful planning leads to OEM like results. Our choice of smaller resonators also gives us the most freedom and space for positioning.
Aluminum Oil Pan Upgrade
While our Project GLI may not be the lowest out there, we still have had more than enough encounters with surprise road debris and potholes that we decided that while we had the car up on the lift it would be a good time upgrade from the notoriously brittle OEM plastic oil pan to this aluminum replacement. The pan includes a pre-installed gasket which makes this a pretty much bolt in affair, apart from having to swap over the the oil sensor. We now have a bit more peace of mind that we can make contact with those random objects jettisoned from pick up trucks without the complete guarantee of a puncture.
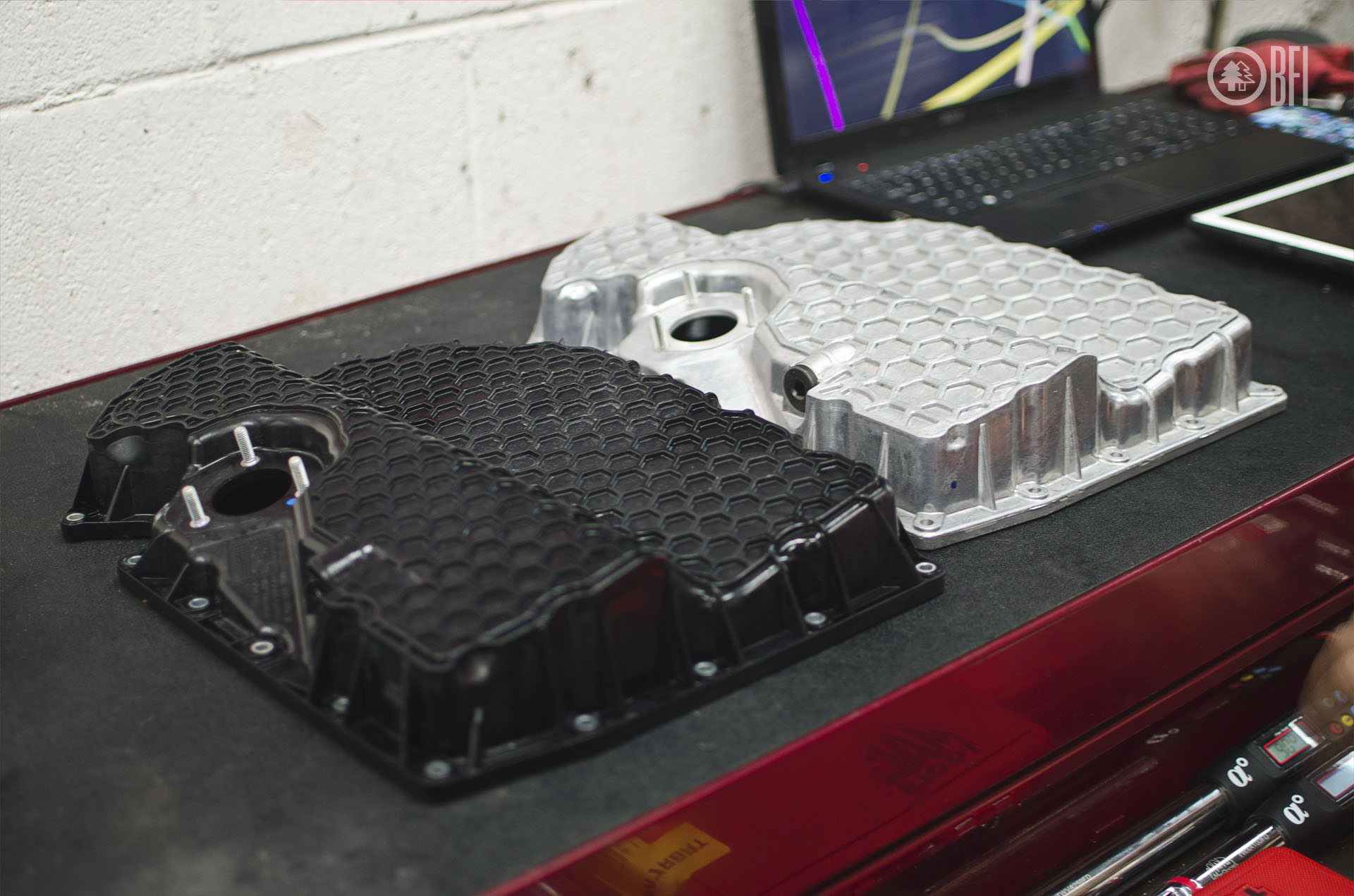

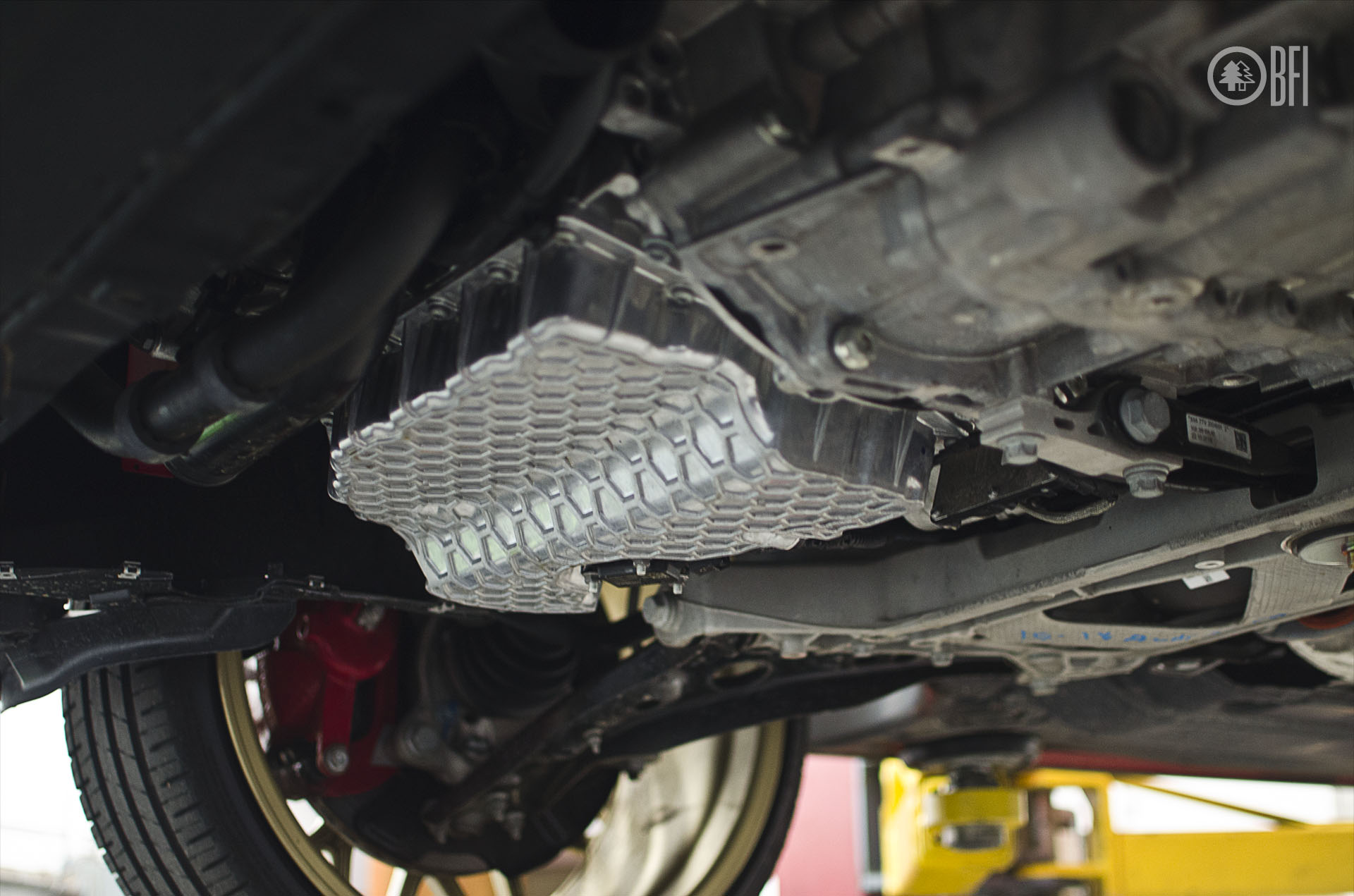
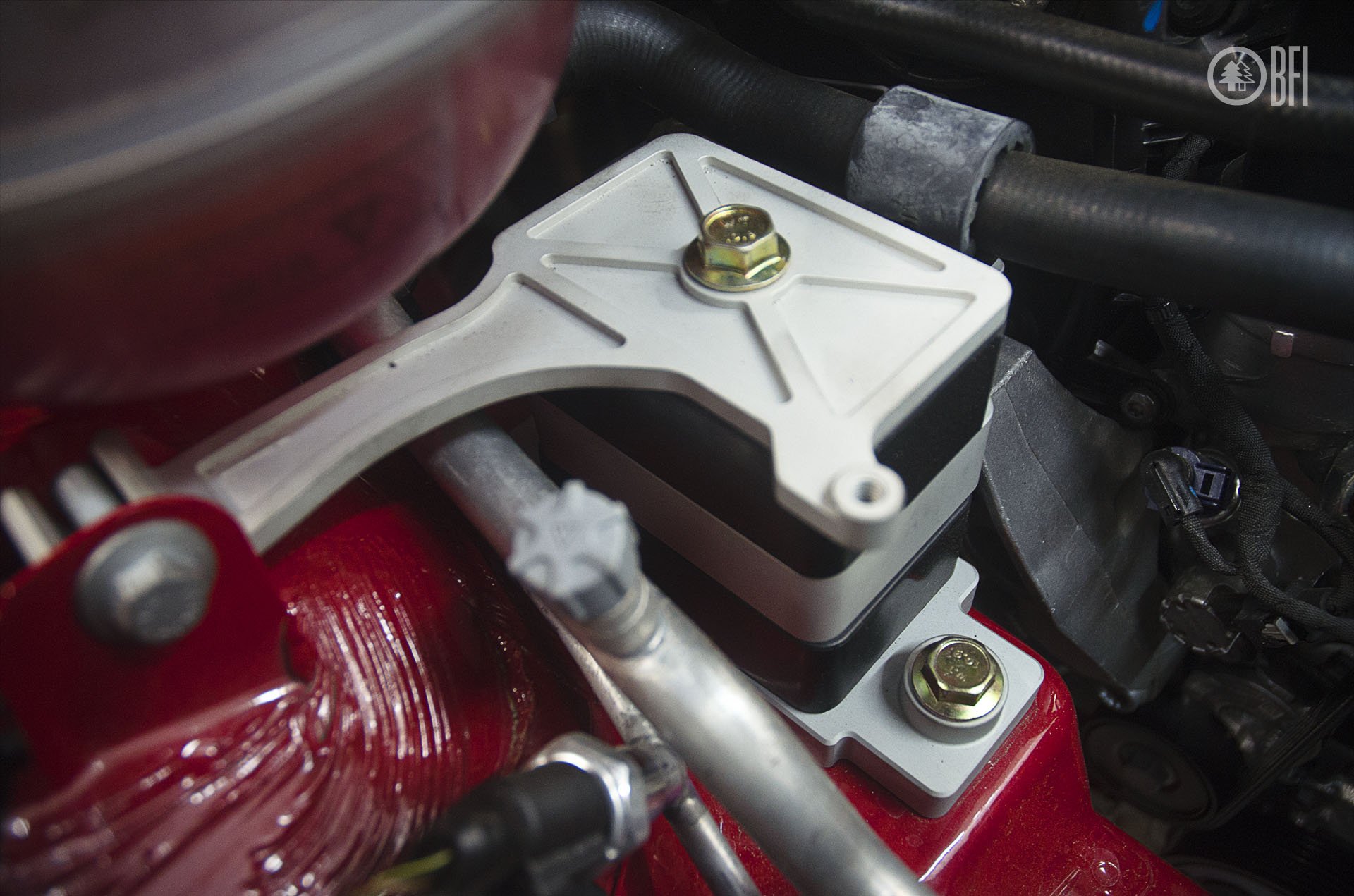
A better look at our Stage 1 Engine Mount. With the bumper removed we were able to get much more up close and personal with it installed in the bay.
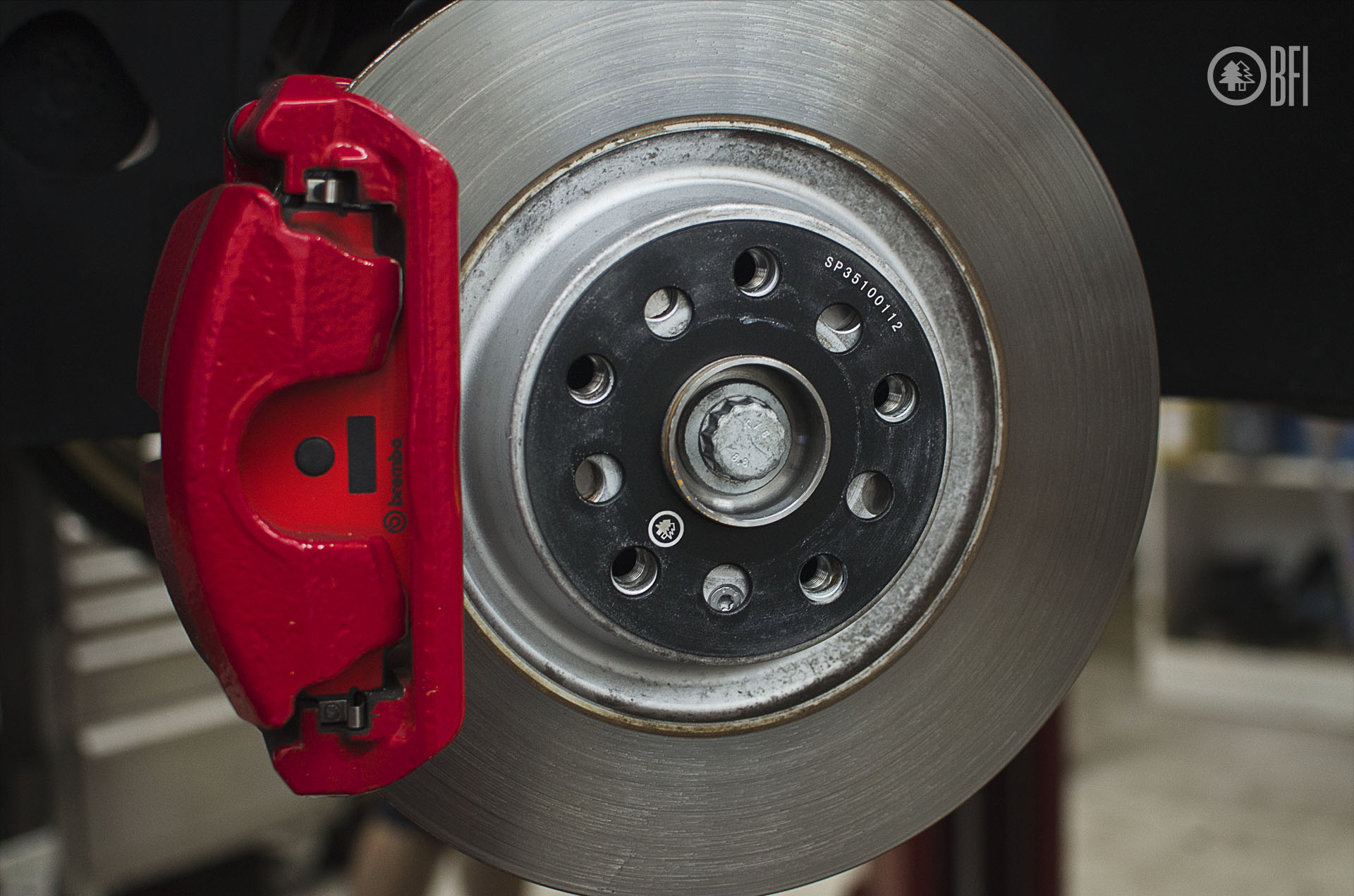
Another look at our BFI Wheel Spacers doing the job to give the best visual appearance while offering crucial clearance at the same time.